Company A used an ERP system built on AcuCOBOL – it was text-based, and while a skilled operator could use it quickly and effectively, it lacked a number of features. The vendor provided an ODBC connector for the system, and I implemented a periodic import into SQL Server. This enabled various extended functionality:
Product Master
I extended the existing product master data by building a system into which extended product data could be imported, including product images. This was implemented via an intranet application, and allowed greater visibility of product data to a wider range of users. Manufacturing staff could print a picture-based Bill of Materials, enabling faster and more accurate assembly.
Order Labels
I created a system with which manufacturing staff could print the required labels for a given order, by entering the order number and the desired quantity of products per packing unit. Settings applied to the products via the product master application allowed the correct label type to be selected, removing the need for operators to make the choice on the factory floor. The labels then functioned as a manufacturing trigger for the various factories, and contained a barcode that was able to be read by a custom-built script in the pre-existing ERP system, simplifying checking into the dispatch area, and the packing outer labels contained customer address data that enabled them to be used directly as shipping labels.
Particular label types could use product images, converted by the intranet into label-printer compatible pictures, to meet the needs of customers who stocked the product in their own stores and needed a visual reference to help in picking the correct product.
Weight Checker
Together with one of the Company’s production engineers, I devised a method of checking assembled product by weight: an application, running on a PC with some connected scales was capable of reading the barcodes on the Order Labels, interrogating the system and by comparing the weighed product to previous iterations of the same product, decide if the recorded weight fell within pre-defined allowances, and either accept or reject the product on that basis. The application could prioritise weight comparisons based on the packed quantity, in order to allow for the differing packaging requirements, and presented the user with a graphical representation of the measured product’s weight compared to previous measurements. The application was also capable of forcing a check on a numerical basis, e.g., for every 100th scanned product require a manual check.
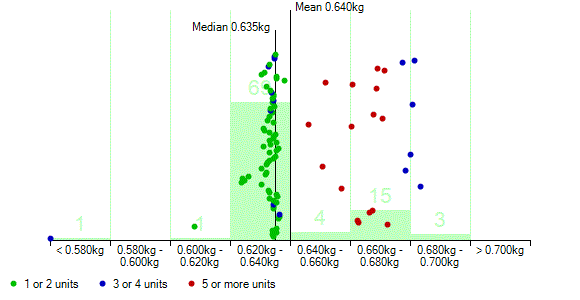
The Company recorded a marked reduction in product returned for missing parts, and when the existing ERP was eventually replaced the application was modified to work with the replacement ERP as no equivalent was available on the market.
Sales Reports
I assembled a suite of reports that could be generated on a daily basis, eliminating the need for administrative staff to create the reports. The benefits of this system saw the deployment of an equivalent system for one of the Company’s sister companies in Australia.
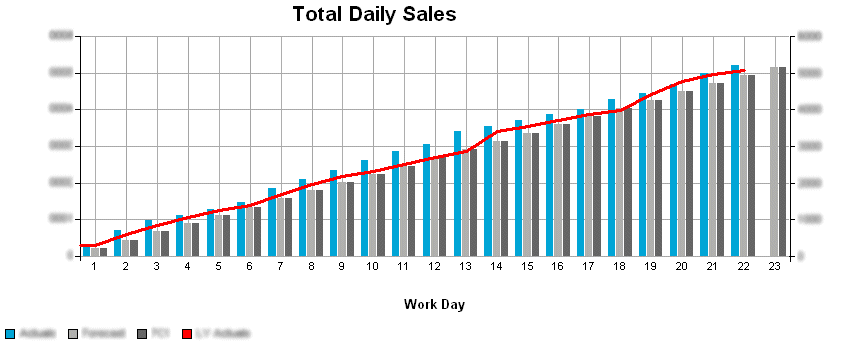
NB: I was employed by Company A for most of the duration of these projects.